
Xi’an Huan-tai Technology & Development Corp., LTD.
Metal Casting and Export Division
-
Our professional NDT inspection team assures castings quality
Date:0000-00-00With 20 years experience on many mechanical parts, we help our customers ensure the internal quality and safety of the products, and help our customers avoid the potential catastrophic failure and financial losses. Now we'd like to provide our non-destructive test (NDT) service for you if you want to have your products checked by magnetic particle examination (MPE), ultrasonic examination (UE), liquid penetration examination (LPE). Our certificated NDT inspectors are proficient in both national and international standards, such as ASTM A609, ASTM E446, ASTM E186, ASTM E125, EN 12680, EN 10228-4, ASTM A388 and so on, and we can carry out NDT at your facility or any other localities as you request.
If you're looking for professional NDT service, please feel free to contact us. And if you're looking for a reliable supplier for mechanical products for crushers, please contact us as well, we'll give you our best quotation.
-
The Introduction of Our Dross Processing
Date:2017-09-11Our quote is based on his knowledge of your facility and it’s dross. We have been supplying the highest quality dross pans to the aluminum industry for over 20 years now. All of the major players in aluminum melting and casting have purchased our quality castings. Last year we started quoting dross presses based on Mr. Roth’s extensive knowledge of manufacturing this equipment. Our equipment is at the same quality level as our castings and at the cutting edge of this technology.
Based on his knowledge of your operation, the unique characteristic of our pan design allows for a significant degree of cooling contact between the dross and cast steel. The number of holes and the double counter sink design allows for the maximum drain possible, without dross sticking in these holes. The distance between the skim and and sow mold is looked at closely to allow large drain volumes without the pans freezing together.
The cooling cycle for these pans will be approximately two hours before the material can be rotated out of the pans. The large pan mass is critical to this result.
Our customers' original use of the press was a failure for two reasons. First there were not enough presses for an operation of your size. If a dross pan sets for more than 15 minutes with your type and temperature of dross the cooling and plating action that is the main benefit of pressing will not be achievable. The operators become frustrated at not seeing results when several pans are stacked up in front of a press and they are processing cold materials without results. In simple terms they stop doing what they see as a waste of time in their busy day. This was evident in your first efforts at pressing. The same failure would occur this time around if you purchase only one press per location as in our customers' tender request. For this reason, we are respectfully quoting two presses per location. With one press, you will achieve the same results of your last experience at his technology.
The design and volume of our pans and press head will ensure the fastest cooling, highest drain and significant plating action of the pressed dross possible. We have designed them specifically to your furnaces, dross volumes and fork truck capabilities. The Tardis pans were a very poor design. The had one hole for draining that always plugged up because of its configuration. The single chamber pan volume did not support cooling or the best plating action possible when pressing.
The most important part of the pressing process is the casting design of the pan and head. We focus on this area. Providing a high quality, simple low maintenance press to utilize the castings.
We are available by phone, e mail or conference call to answer any of your questions.
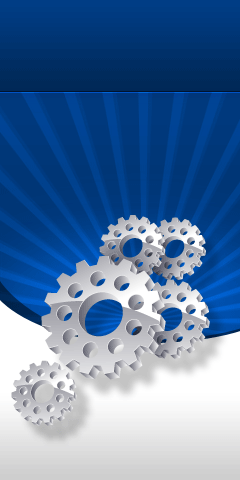
-
-
Truck & Semi Truck Parts
-
-
-
Railways Machinery Parts
-